Das Internet of Things bezeichnet Technologien, die physische Gegenstände mit digitalen Systemen verbinden und mit Hilfe von Informations- und Kommunikationstechniken (z.B. Sensoren) miteinander kommunizieren lassen. Physische Gegenstände, wie zum Beispiel Lagerregale oder Transportfahrzeuge können durch IoT auch untereinander Informationen austauschen, etwa über Auslastung oder Position. Wird 2022 das Jahr von IoT?
Das Internet of Things (Internet der Dinge) bezeichnet Technologien, die physische Gegenstände mit digitalen Systemen oder dem Internet verbinden und mit Hilfe von Informations- und Kommunikationstechniken (z.B. Sensoren) Kommunikation untereinander oder mit Software-Anwendungen ermöglichen.
Ohne Digitalisierung geht nichts mehr im industriellen Bereich
In den vergangenen Jahren musste sich die Industrie extrem dynamischen Veränderungen stellen, mit drastischen Folgen für nahezu alle Geschäftsbereiche. Somit haben sich viele Rahmenbedingungen grundlegend geändert, die zu deutlich gestiegenen Anforderungen für die Fachbereiche, wie zum Beispiel in der Produktion, Logistik und Instandhaltung geführt haben. Neben dem Fachkräftemangel sind kontinuierlich voranschreitende Entwicklungen in den Bereichen Industrie 4.0, Automatisierung und Mobility die Treiber dieser Entwicklung und haben gegenwärtig bei Produktionsunternehmen höchste Priorität. So nehmen immer mehr IT-Themen Einzug in unterschiedlichste Fachbereiche, die lange Zeit völlig anlog und ohne Software auskamen und arbeiteten.
Stetig steigende Komplexität von Prozessen und Abläufen erfordern zwingend systemische Unterstützung
Digitale Prozesse und Workflows vernetzen abteilungsübergreifend Arbeitsabläufe und sorgen im Ergebnis für ein reibungsloses Zusammenspiel sowie für mehr Produktivität. Hierbei ist es u.a. erforderlich, Ressourcenplanung, Materialdisposition, Ersatzteillager und Bestellungsprozesse in Echtzeit zu synchronisieren. Darüber hinaus stellen die aktuellen Lieferengpässe und Ressourcenknappheit speziell produzierende Unternehmen vor große Herausforderungen. Ohne eine systemtechnische Unterstützung, gesteuert aus dem ERP (z.B. SAP), sind synchronisierte und transaktionssichere Abläufe nicht mehr zu gewährleisten. Dabei sind die Bereiche Produktion und Instandhaltung aufgrund von Schnittstellen (Personal, Material, Technik usw.) besonders gefordert. Es gilt, unterschiedliche Unternehmensprozesse mithilfe einer durchgehenden Digitalisierung zu vereinfachen und zu automatisieren, Prozesse zu optimieren und dabei gleichzeitig den Fokus auf die Wertschöpfung zu legen.
Industrie 4.0 Plattform: Der Motor für Digitalisierungsprojekte
Eine der grundlegenden Voraussetzungen, um digitale sowie mobile Prozesse zu ermöglichen, ist eine Vernetzung aller relevanten Systeme. Dabei übernimmt eine Industrie 4.0 Plattform (Membrain-IoT) die bidirektionale Kommunikation zwischen Back-End- und Front-End-System sowie zwischen Maschinen und Steuerungen. Diese Datendrehscheibe stellt benötigte Daten dem Anwender mobil und vor Ort (z.B. an der zu reparierenden Maschine) bereit. Erledigte Arbeiten werden direkt per App auf mobilen Geräten (z.B. Smartphone, Tablet PCs und Industriescanner) dokumentiert und umgehend zurück in das führende System (SAP) gebucht. Auch die Echtzeitfähigkeit der Lösung ist unabdingbar, denn sie stellt sicher, dass immer der tatsächliche und aktuelle Stand systemseitig verfügbar ist. Nur so kann man komplexe Unternehmensprozesse automatisieren und nahtlos auf höchstem Niveau gewährleisten.
Industrie 4.0 bezeichnet die umfassende Digitalisierung der industriellen Produktion, um sie für die Zukunft besser zu rüsten. Die industrielle Produktion soll dabei mit moderner Informations- und Kommunikationstechnik verzahnt werden. Technische Grundlage hierfür sind intelligente und digital vernetzte Systeme.
Digitale Trends & Applikationen aus der Industrie
IoT hebt die mobile Instandhaltung auf das nächste Level
Besonders in der Serienfertigung (Assembling) sind unterbrechungsfreie Prozesse entscheidend. Eine möglichst hohe technische Verfügbarkeit von Maschinen und Anlagen ist das oberste Ziel der Instandhaltung – Maschinenausfälle sowie Produktionsunterbrechungen müssen daher verhindert bzw. auf ein Minimum reduziert werden. Herkömmliche, papiergebundene und manuelle Prozesse geraten schnell an ihre Grenzen. Digitalisierung automatisiert die Instandhaltung, besonders in Bereichen mit stark standardisierten Prozessen und einem hohen Grad an klar definierten Abläufen. Ein Zugriff in Echtzeit auf kritische Anlagen und Maschinen ermöglicht unmittelbare Reaktionen auf Ereignisse. Im Vordergrund steht der Ansatz, transaktionale Aufgaben durch Technologie zu automatisieren und abzuwickeln, um so die gewonnenen Ressourcen für Tätigkeiten mit höherer Wertschöpfung nutzen zu können. Dank der digitalen Lösung erhält der Instandhalter ein leistungsstarkes Tool, mit dem er seinen tagtäglichen Job effizienter gestalten kann. Instandhaltungsaufträge werden mobil per App zugestellt, können in Echtzeit neu priorisiert und nach Erledigung unmittelbar rückgemeldet werden.
Ebenfalls bietet der Zugriff auf notwendige Dokumente ein einfaches und schnelles Erledigen von Instandhaltungsaufträgen. Darüber hinaus fällt die zeitaufwändige und lästige Dokumentationspflicht für den Instandhalter weg, da dies die App im Hintergrund erledigt. Durch diese Automatisierung des Instandhaltungsprozesses können Arbeitszeiten effizienter genutzt und menschliche Dokumentationsfehler eliminiert werden.
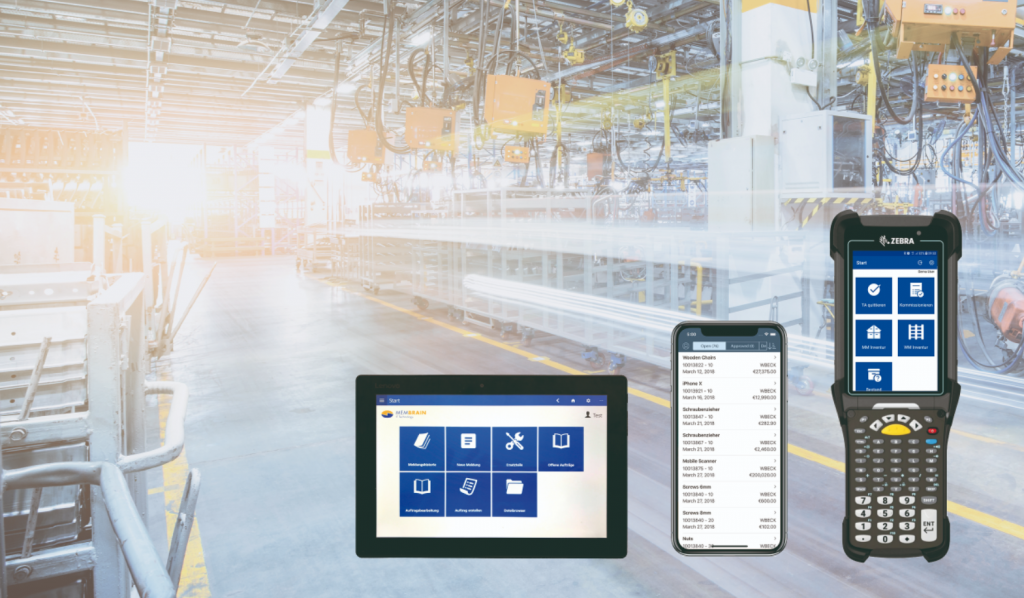
IoT: Kennzahlgetriebene Produktionsprozesse für eine kontinuierliche Verbesserung
Besonders im Produktionsumfeld bekommen betriebswirtschaftliche Kennzahlen eine immer entscheidendere Bedeutung sowie eine größere Wichtigkeit. IoT bzw. Daten aus Steuerungen und Maschinen bieten dabei die notwendige Informationsbasis. Besonders für die Instandhaltung gibt es ein großes Spektrum solcher KPIs. Die wichtigsten dabei sind:
- OEE (Overall Equipment Effectiveness, Gesamtanlageneffektivität),
- TV (Technische Verfügbarkeit Maschinen),
- MTBF (Mean time between failures, durchschnittliche Zeit zwischen den Störungen),
- MTTR (Mean time to repair, Durchschnittliche Zeit der Entstörungen)
Mit diesen betriebswirtschaftlichen Kennzahlen kann man die Produktivität und etwaige Verluste durch Ausfälle von technischen Anlagen oder Maschinen messen. Dabei gilt: Je höher die erzielte Gesamtanlageneffektivität einer Anlage, desto größer ist das Leistungspotential, das dem Produktionsprozess zur Verfügung gestellt wird. Die Maximierung der Gesamtanlageneffektivität gehört damit zu den obersten formalen Zielen auch bei der Instandhaltung von Anlagen.
Erste Erfahrungen aus der Praxis zeigen, dass diese Kennzahlen immer mehr im Fokus stehen und umfangreich analysiert werden: Ausfallzeiten, Störgründe sowie produzierte Mengen (Vergleich der Gutmengen und des Ausschusses und eventuelle Abweichungen). Um eine bessere Aussagefähigkeit dieser Reports zu bekommen, werden außerdem entsprechende produktionsspezifische Merkmale erfasst und interpretiert. Dazu gehören vorrangig die verschiedenen Produktionslinien für ein bestimmtes Produkt (inkl. verschiedener Standorte der jeweiligen Produktionsanlage sowie der Produktionsperiode, also dem Tag oder der Schicht der Produktion). Nach erfolgter Festlegung bzw. Ermittlung dieser Prozess- und Produktionskennzahlen können Unternehmen die Ergebnisse bewerten, um Verbesserungspotenziale zu erkennen und entsprechende Maßnahmen einzuleiten. So lässt sich ein höheres Produktivitätsniveau erreichen, aufrechterhalten und langfristig der Unternehmenserfolg sichern.
Die digitale Fabrik, IoT und der Factory Monitor
Eine Anbindung des Maschinenparks ermöglicht eine Echtzeitüberwachung per Factory Monitor. Kritische Maschinen melden kontinuierlich ihren „Gesundheitszustand“, Servicebedarf oder mögliche Störungen (Predictive Maintenance). Instandhaltungsaufträge man man beispielsweise bequem per App direkt vom mobilen Gerät (Smartphone oder Tablet-PC) des Instandhalters bearbeiten und verwalten, wobei man die gesamte Kommunikation (Rückmeldung/neue Aufträge/Ersatzteile) in der App, komplett ohne Papier, abgewickelt. Auch eine schlechte Erreichbarkeit der Mitarbeiter, die Komplexität der Auftragszuteilungen sowie der enorme Verwaltungsaufwand lassen sich deutlich optimieren. Im Ergebnis werden menschliche Fehler reduziert, eine 100%ige Transaktionssicherheit gewährleistet und die gesamte Dokumentation automatisch im Hintergrund durchgeführt.
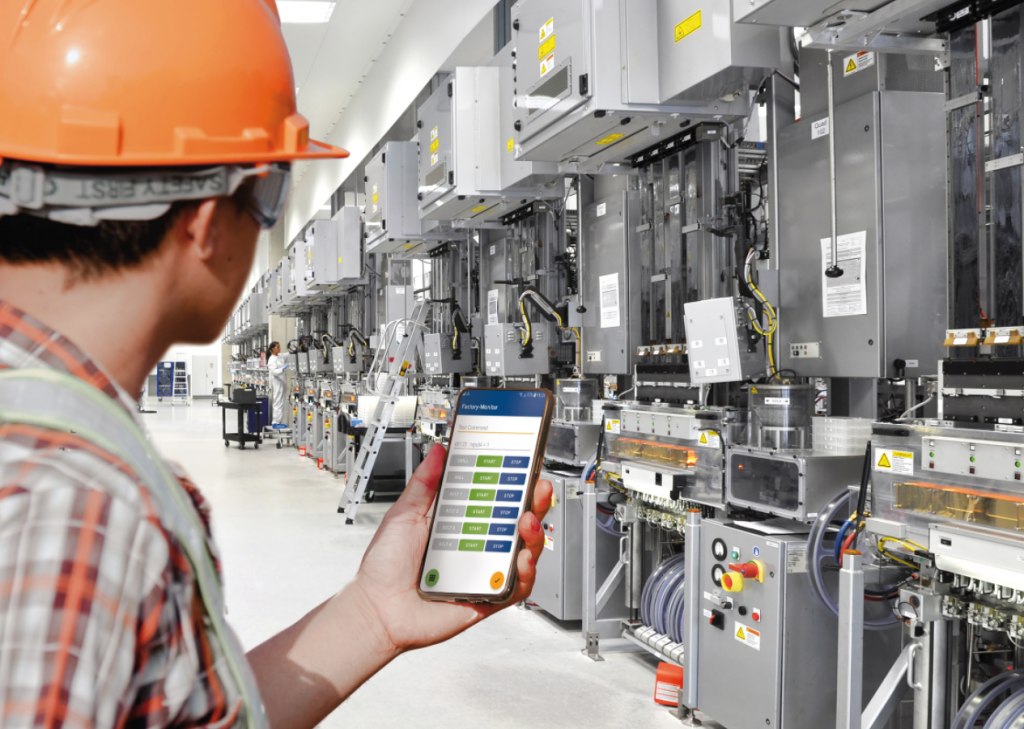
Der Factory Monitor visualisiert den Live-Zustand einzelner Maschinen grafisch. Bei vordefinierten Ereignissen (z. B. Über- oder Unterschreitung eines Grenzwertes) generieren sich automatisch Meldungen und schreiben sie direkt ins führende ERP-System (SAP). Das kann zum Beispiel eine E-Mail-Benachrichtigung an den Fertigungsleiter sein. Ebenfalls kann auch ein vordefiniertes Event (z.B. Maschinenstopp) ausgelöst werden. Störgründe für Maschinenstillstände werden für historische Daten und Analysezwecke direkt mitdokumentiert. Dazu werden die im ERP-System hinterlegten Störgründe pro Maschine bzw. Maschinengruppe herangezogen. Schließlich sorgt der Einsatz von Apps nicht nur für eine Echtzeitkommunikation, sondern auch für eine lückenlose Datendokumentation im System. Dabei liefert die Schnittstelle wertvolle Maschinendaten wie z.B. Produktionszeiten und Stillstände, Prozessdaten (z.B. Temperatur und Druck) sowie Energiedaten (Strom- und Wasserverbrauch, Luftdruck, etc.). Diese erhobenen Daten lassen sich darüber hinaus auch präventiv verwenden, um beispielsweise einen drohenden Maschinenausfall zu verhindern.
Ganzheitlicher Digitalisierungsansatz ist entscheidend
Ein entscheidender Erfolgsfaktor für IoT-Projekte ist eine Industrie 4.0 Plattform (Membrain-IoT). Diese garantiert Transaktionssicherheit im ERP-System, unterbrechungsfreies Arbeiten, lückenlose Rückverfolgbarkeit sowie das Sicherstellen von Workflows. Ihre flexible Software-Architektur, die Modularität, Echtzeitfähigkeit und Skalierbarkeit sorgen für maximale Zukunftsfähigkeit. Generell aber gilt: Ein ganzheitlicher Ansatz bei der Digitalisierungsstrategie ist entscheidend. Denn nur so lassen sich Medienbrüche sowie menschliche Fehler eliminieren. Insellösungen schaffen nur punktuelle Effizienzsteigerung aber keine durchgehende Digitalisierung. Nur der ganzheitliche Ansatz mit Vernetzung aller Systeme erreicht eine Optimierung der gesamten Prozesskette, von der Materialwirtschaft über die Fertigung bis hin zur Logistik.